Corrosion is a silent but relentless threat to architectural projects, compromising the structural integrity of buildings and leading to significant maintenance challenges. Metal preservation is a critical aspect of ensuring the longevity and durability of valuable assets in a number of different industries. Whether it's steel structures like bridges, industrial equipment like HVAC cooling towers, or marine vessels like commercial fishing boats, exposure to environmental elements can lead to corrosion and degradation over time, compromising both the aesthetics and functionality of metal surfaces.
Over time, exposure to the elements can cause metal components to deteriorate, resulting in costly structural steel repair and reduced building longevity. For architects and builders, understanding and addressing corrosion is crucial to ensuring the durability and safety of their designs. Using a cold galvanizing compound is the key to prolonged metal life!
By choosing the right corrosion protection, such as ZRC’s galvanized paint, you can safeguard your projects against the damaging effects of corrosion, ultimately reducing maintenance costs and extending the life of the structure.
This corrosion protection is crucial for maintaining architectural integrity because it prevents the deterioration of metal components that are essential to a building's strength and stability. Without proper protection, corrosion can weaken these components, leading to structural failures and compromising the safety of the entire project.
Additionally, effective corrosion protection is cost-effective. It reduces the need for frequent repairs, minimizes long-term maintenance expenses, and extends the lifespan of the building, ensuring a better return on investment. If the metal is not regularly cleaned and dried, moisture can accumulate on the surface and lead to rust. Once it reaches a “point of no return,” you will not be able to salvage a rusty steel structure. The structure will need to be totally replaced or require costly repairs years before it would have otherwise. Spend a little now, save a lot later on!
In this guide, you will learn about the critical role that cold galvanized paint plays in protecting architectural structures from corrosion, offering a durable, long-lasting solution that prevents metal deterioration. The guide will highlight the key benefits of using cold galvanized paint, such as its ease of application, superior quality, and unmatched corrosion resistance. It will also explain why ZRC’s galvanized paint stands out as the go-to choice for architects, thanks to its proven performance, industry-leading quality, and trusted reputation in the field.
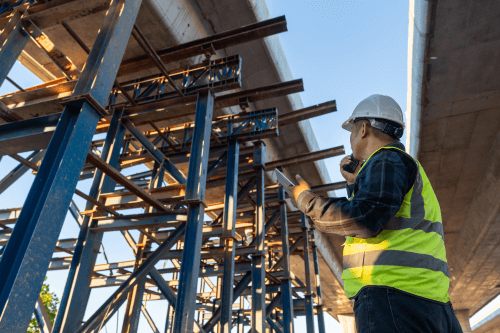
Understanding Cold Galvanizing Compound
A cold galvanizing compound is a protective coating applied to metal surfaces to prevent corrosion. Unlike traditional hot-dip galvanizing, which involves immersing the metal in molten zinc, cold galvanizing is a simpler process that can be applied directly to the metal without the need for heat. This makes it an ideal solution for on-site repairs, touch-ups, and applications where hot-dip galvanizing is impractical.
The Components of Rust Paint
The two primary components of cold galvanizing compounds are
- zinc dust
- resin
Zinc dust is the active ingredient that provides the coating's corrosion-resistant properties. When applied, the zinc particles create a physical barrier on the metal surface, shielding it from moisture and other corrosive elements. Additionally, zinc has a sacrificial quality, meaning it will corrode before the underlying metal, offering further protection.
The resin in the galvanized paint compound acts as a binder, holding the zinc particles together and ensuring they adhere to the metal surface. The type of resin used can vary, but it is typically selected for its durability and ability to withstand environmental factors such as UV exposure, temperature fluctuations, and chemical exposure. Together, zinc dust and resin form a robust, long-lasting coating that effectively protects metal surfaces from corrosion.
Preventing Rust: Application Options for Galvanized Paint
Cold galvanizing compounds can be applied using various methods, depending on the specific needs of the project and the area being treated. The most common application methods are:
Each method ensures that the cold galvanizing compound adheres properly to the metal surface, providing a durable and protective layer against corrosion. The choice of application method often depends on the size, shape, and condition of the metal surface, as well as the specific requirements of the project.
The Role of Cold Galvanizing Compound in Corrosion Protection
Cold galvanizing involves a chemical and physical process that provides robust protection against corrosion. When a cold galvanizing compound is applied to a metal surface, the zinc dust within the compound plays a crucial role in safeguarding the underlying metal. Zinc is a highly reactive metal, and its primary function in cold galvanizing is to act as a sacrificial anode — a concept rooted in electrochemistry.
The sacrificial nature of zinc means that it corrodes before the underlying metal does. When moisture, oxygen, or other corrosive elements come into contact with the zinc-coated surface, the zinc reacts with these elements to form zinc oxide, which further reacts to create zinc carbonate. This reaction consumes the zinc, but in doing so, it protects the base metal from corrosion. Essentially, the zinc in rust paint sacrifices itself to shield the metal beneath, ensuring that the structural integrity of the metal remains intact even in harsh environments.
In addition to this sacrificial protection, the cold galvanizing compound forms a physical barrier on the metal surface. The zinc particles, bound together by the resin in the compound, create a dense, protective layer that physically blocks moisture, chemicals, and other corrosive agents from reaching the metal. This barrier effect is critical because it prevents the initial contact between the metal and corrosive elements, significantly reducing the risk of rust and degradation.
As well, the resin component in the cold galvanizing compound enhances this protective layer by providing strong adhesion to the metal surface and increasing the coating's durability. The resin helps the zinc particles bond effectively to the metal, ensuring that the protective layer remains intact even under environmental stress, such as temperature fluctuations or physical abrasion. Together, these chemical and physical processes work in tandem to provide long-lasting corrosion protection, making cold galvanizing an effective solution for preserving the integrity and longevity of metal structures.
The Benefits of ZRC Galvanizing Compound Over Other Methods
When comparing cold galvanizing to other corrosion protection methods like hot-dip galvanizing and regular paint, it's important to consider factors such as application, durability, and effectiveness.
Cold Galvanizing vs. Hot-Dip Galvanizing
Application:
Cold galvanizing is a much simpler and more versatile process than hot-dip galvanizing. It can be applied directly to metal surfaces using brushes, sprays, or rollers, making it ideal for on-site repairs and projects where hot-dip galvanizing is impractical. Hot-dip galvanizing, on the other hand, involves immersing the metal in molten zinc at high temperatures, which requires specialized facilities and equipment.
Durability
Hot-dip galvanizing provides a thick zinc coating, typically resulting in superior long-term protection, especially in highly corrosive environments. The zinc layer from hot-dip galvanizing is resilient to physical damage and can offer decades of protection. However, cold galvanizing still offers excellent protection, particularly for maintenance, touch-ups, and projects where hot-dip galvanizing isn't feasible.
Effectiveness
Both methods rely on zinc's sacrificial protection to prevent corrosion. They are similar in terms of effectiveness, so you don’t have to give up how well a product works in order to take advantage of the convenience of cold galvanized paint.
Application:
Cold galvanizing is a much simpler and more versatile process than hot-dip galvanizing. It can be applied directly to metal surfaces using brushes, sprays, or rollers, making it ideal for on-site repairs and projects where hot-dip galvanizing is impractical. Hot-dip galvanizing, on the other hand, involves immersing the metal in molten zinc at high temperatures, which requires specialized facilities and equipment.
Durability
Hot-dip galvanizing provides a thick zinc coating, typically resulting in superior long-term protection, especially in highly corrosive environments. The zinc layer from hot-dip galvanizing is resilient to physical damage and can offer decades of protection. However, cold galvanizing still offers excellent protection, particularly for maintenance, touch-ups, and projects where hot-dip galvanizing isn't feasible.
Effectiveness
Both methods rely on zinc's sacrificial protection to prevent corrosion. They are similar in terms of effectiveness, so you don’t have to give up how well a product works in order to take advantage of the convenience of cold galvanized paint.
Cold Galvanizing vs. Regular Paint
Application
Both cold galvanizing and regular paint can be applied with similar methods — brushing or spraying. However, cold galvanizing is specifically designed to provide corrosion protection, while regular paint is typically used for aesthetic purposes and general surface protection.
Durability
Regular paint provides a protective layer against environmental elements, but it lacks the sacrificial protection that cold galvanizing offers. Over time, regular paint will chip, crack, or peel, exposing the metal beneath to corrosion. Cold galvanizing, with its zinc-rich formulation, offers much stronger protection by forming a durable barrier and actively preventing corrosion through zinc's sacrificial action.
Effectiveness
Cold galvanizing is far more effective in preventing corrosion using regular paint for rusty metal. While paint primarily serves as a barrier, cold galvanizing combines this barrier with the chemical protection of zinc, making it a superior choice for long-term metal preservation, particularly in industrial or outdoor environments.
Application
Both cold galvanizing and regular paint can be applied with similar methods — brushing or spraying. However, cold galvanizing is specifically designed to provide corrosion protection, while regular paint is typically used for aesthetic purposes and general surface protection.
Durability
Regular paint provides a protective layer against environmental elements, but it lacks the sacrificial protection that cold galvanizing offers. Over time, regular paint will chip, crack, or peel, exposing the metal beneath to corrosion. Cold galvanizing, with its zinc-rich formulation, offers much stronger protection by forming a durable barrier and actively preventing corrosion through zinc's sacrificial action.
Effectiveness
Cold galvanizing is far more effective in preventing corrosion using regular paint for rusty metal. While paint primarily serves as a barrier, cold galvanizing combines this barrier with the chemical protection of zinc, making it a superior choice for long-term metal preservation, particularly in industrial or outdoor environments.
The Importance of Specifying High-Quality Cold Galvanizing Compound
High-quality cold galvanizing compounds are essential for providing superior protection and ensuring longer-lasting results in corrosion prevention. The quality of the compound directly impacts its effectiveness in safeguarding metal surfaces from the damaging effects of corrosion, particularly in harsh environments.
One of the key factors in a high-quality cold galvanizing compound is the concentration and purity of zinc dust. A higher zinc content typically translates to better sacrificial protection, where the zinc corrodes in place of the underlying metal, creating a strong, self-healing barrier against rust. High-purity zinc ensures that the protective layer is more consistent and effective, reducing the likelihood of weak spots that could expose the metal to corrosion.
Additionally, high-quality compounds use advanced resins that offer excellent adhesion and durability. These resins not only bind the zinc particles together but also ensure that the coating adheres firmly to the metal surface, even under challenging conditions like temperature fluctuations, moisture, and UV exposure. This strong bond prevents the coating from peeling, cracking, or chipping, which are common issues with lower-quality products.
Moreover, superior cold galvanizing compounds are formulated to resist environmental wear and tear, providing extended protection over time. They are designed to maintain their integrity and effectiveness even in aggressive industrial or coastal environments, where corrosion risks are higher. This longevity reduces the need for frequent reapplication, saving time and maintenance costs while ensuring the structure remains protected for years.
Compliance With Corrosion Preventive Compound Standards
Compliance with industry standards, such as SSPC Paint 20, is a critical factor when selecting a cold galvanizing compound, as it ensures the product meets rigorous quality and performance criteria essential for effective corrosion protection.
Established by the Society for Protective Coatings (SSPC), SSPC Paint 20 is a widely recognized standard that specifically addresses zinc-rich coatings, including cold galvanizing compounds. This standard outlines the requirements for zinc content, adhesion, and overall performance, ensuring that products meeting SSPC-Paint 20 are of the highest quality and capable of delivering reliable protection in demanding environments.
To comply with SSPC-Paint 20, a cold galvanizing compound must contain a minimum percentage of zinc by weight in the dry film. This high zinc content is crucial for cold galvanize paint because it ensures that the compound provides robust sacrificial protection, where the zinc corrodes instead of the underlying metal. The standard also dictates that the zinc particles must be evenly distributed and sufficiently pure, contributing to a more effective and consistent protective coating.
In addition to zinc content, SSPC Paint 20 sets strict guidelines for the adhesion and durability of the coating. A compliant cold galvanizing compound must adhere well to the metal substrate, resist environmental stressors such as moisture and UV radiation, and maintain its protective properties over time. This ensures that the coating remains intact and continues to protect the metal surface against corrosion, even in harsh conditions.
Choosing a cold galvanizing compound that complies with SSPC Paint 20 or similar standards provides confidence that the product will perform as expected, offering long-lasting protection and reducing the risk of corrosion-related issues. This compliance also ensures that the product meets industry benchmarks, making it suitable for use in a wide range of applications, from industrial to architectural projects.
Cost-Effectiveness
Choosing the right cold galvanizing product is a critical decision that can significantly impact both the maintenance costs and the lifespan of structures. High-quality cold galvanizing compounds provide durable, long-lasting protection against corrosion, which is one of the primary causes of metal deterioration. By effectively preventing rust and corrosion, these compounds help maintain the structural integrity of metal components, reducing the need for frequent repairs or replacements.
When a metal structure is well-protected from corrosion, the overall maintenance requirements decrease. Routine maintenance tasks, such as inspecting for rust or reapplying protective coatings, become less frequent and less costly. This reduction in maintenance needs not only lowers the direct costs associated with labor and materials but also minimizes downtime, keeping the structure in optimal condition and functional for longer periods. Over time, these savings can add up to a significant reduction in the total cost of ownership.
It is also worth noting that by extending the lifespan of metal structures, the right cold galvanizing product helps to maximize the return on investment. Structures that are protected from corrosion last longer and perform better, delaying the need for costly replacements or extensive refurbishments. This longevity is particularly important for large-scale projects or infrastructure, where the financial and operational impacts of corrosion-related damage can be substantial.
Why ZRC’s Cold Galvanizing Compound Stands Out in The Corrosion Prevention Industry
Knowing how to prevent steel from rusting by using a cold galvanizing compound is only the beginning. Not all products will deliver the results you’re looking for. Specifying a high-quality cold galvanizing compound is crucial for achieving the best possible corrosion protection. ZRC delivers more reliable and durable performance, ensuring that metal structures remain intact and corrosion-free for an extended period. That is why so many architects specify ZRC by name in their spec sheets.
Proven Performance
ZRC has established itself as a leader in the corrosion prevention industry, boasting a remarkable track record of over 70 years of pioneering expertise. As industry innovators, ZRC has consistently set the standard for high-quality cold galvanizing compounds, earning a reputation for excellence and reliability.
Our extensive experience and commitment to cutting-edge technology have made us the go-to choice for professionals seeking superior corrosion protection. With decades of proven success, ZRC continues to lead the way, providing trusted solutions that protect structures and ensure long-lasting durability!
Superior Formulation
ZRC’s formulation stands out from competitors due to its superior blend of high-purity zinc dust and advanced resin technology, ensuring unmatched corrosion protection and durability. Our cold galvanizing compounds are meticulously engineered to deliver a higher zinc content, enhancing the sacrificial protection that prevents rust and extends the lifespan of metal surfaces. The unique resin system in ZRC’s products not only ensures excellent adhesion and flexibility but also provides exceptional resistance to environmental stressors such as UV exposure and moisture. This combination of high-performance ingredients and innovative formulation techniques positions ZRC as a leader in the industry, offering a product that delivers reliable, long-lasting protection in even the most demanding conditions.
High Zinc Content
ZRC’s high zinc content is a key factor in delivering exceptional corrosion protection. Zinc's sacrificial properties are central to its effectiveness; it corrodes before the underlying metal, thus preserving the structural integrity of the base material.
By utilizing a high concentration of pure zinc dust, ZRC ensures a more robust protective layer that offers superior resistance to rust and degradation. This elevated zinc content enhances the compound's ability to create a dense, protective coating that shields the metal from moisture and corrosive elements, thereby extending the lifespan of the structure and reducing the need for frequent maintenance. This commitment to high-quality zinc underscores ZRC’s dedication to providing reliable, long-lasting corrosion solutions.
Ease of Application
ZRC’s Cold Galvanizing Compound is designed with user-friendliness and versatility in mind, making it an ideal choice for a wide range of applications. Its easy application process allows for seamless use with brushes, sprays, or rollers, accommodating both large-scale projects and detailed touch-ups.
The galvanized paint’s quick drying time and excellent adhesion ensure a smooth, hassle-free application that integrates well with existing metal surfaces. Additionally, ZRC’s formulation is adaptable to various environments and conditions, providing effective corrosion protection across diverse settings, from industrial sites to architectural projects. This versatility and ease of use make ZRC’s product a practical solution for professionals seeking reliable and efficient corrosion control.
Key Advantages of Specifying ZRC by Name
Brand Reliability
ZRC’s unwavering commitment to quality and consistency is exemplified by our ISO 9000 certification, which underscores our dedication to maintaining the highest standards in every aspect of our manufacturing process. This internationally recognized certification highlights our rigorous quality control procedures and continuous improvement efforts, ensuring that each batch of our cold galvanizing products meets stringent performance criteria. Not only that, we actually exceed the requirements of ASTM A780.
By adhering to these globally accepted standards, ZRC guarantees that our products deliver reliable, superior corrosion protection with every application. This dedication to excellence ensures that customers can trust ZRC for consistent, high-quality solutions that exceed industry expectations.
Technical Support
When architects choose ZRC, they benefit from comprehensive technical support and resources tailored to their needs. Our dedicated team of experts is readily available to provide guidance on selecting the right product for specific applications and ensure it is used correctly. From detailed product information and application instructions to personalized consultations, ZRC’s support network is committed to helping architects achieve optimal results and address any challenges that may arise. This level of service ensures that every project benefits from our expertise and high-quality solutions.
Dedication to Customer Satisfaction
At ZRC, we are dedicated to ensuring that architects are 100% satisfied with our products and services. We offer personalized consultations before you place your order, providing expert advice to help you select the perfect solution for your project.
Our commitment extends beyond just delivering high-quality products; we strive to ensure that every client receives the support they need throughout the process. From initial consultation to application, our team is here to address your needs and ensure you achieve the best possible results.
Suggested Specification Verbiage for Specifying ZRC Cold Galvanizing Compound by Name
“Organic Zinc-Rich coating containing 95% metallic zinc, by weight in the dried film; recognized under the Component Program of Underwriter's Laboratories, Inc. as an equivalent to hot-dip galvanizing; conforming to Federal Specification DOD-P-21035A (formally MIL-P- 21035A) for repair of hot-dip galvanizing and meeting the requirements of Military Specification MIL-P-26915A USAF Specification for Zinc-Rich Paints; as manufactured by ZRC Worldwide, Marshfield, MA or other facility having been registered to the International Organization for Standardization ISO 9001 standard for quality; or approved equal.”
Practical Tips for Architects
Incorporating ZRC Into Weld Repair Specifications
When incorporating ZRC’s cold galvanizing compound into weld repair specifications, architects should follow these guidelines to ensure effective integration and optimal performance:
Specify Product Requirements: Clearly detail the use of ZRC’s cold galvanizing compound in the project specifications, including the product name, type, and required application methods. Highlight the need for high-quality, zinc-rich coatings to ensure durability and corrosion resistance.
Application Instructions: Include specific instructions for applying the cold galvanizing compound. Specify surface preparation requirements, such as cleaning and degreasing the weld area to ensure proper adhesion. Provide guidelines on the application technique — whether brushing or spraying — and the recommended number of coats.
Performance Standards: Reference relevant industry standards and performance benchmarks that ZRC’s product meets, such as SSPC Paint 20. This ensures that the compound will provide the required level of corrosion protection and meet quality expectations.
Inspection and Testing: Outline the procedures for inspecting and testing the weld repair to ensure that the cold galvanizing compound is applied correctly and effectively. Include any necessary quality control measures, such as verifying the thickness of the coating and checking for proper adhesion.
Coordination With Contractors: Encourage coordination with contractors to ensure they are familiar with ZRC’s cold galvanizing compound and its application requirements. Provide contact information for ZRC’s technical support team, who can offer additional guidance and answer any questions during the repair process.
By incorporating these elements into your project specifications, you can ensure that ZRC’s cold galvanizing compound is used effectively for weld repair projects, providing long-lasting protection and maintaining the structural integrity of the project.
Application Guidelines
By following these simple step-by-step instructions and safety precautions, you can effectively apply cold galvanizing compoun to protect your outdoor metal assets from rust, corrosion, and environmental damage.
#1 Prepare the Work Area: Start by selecting a well-ventilated area for the application process, preferably outdoors. Ensure no spray will blow onto something you don’t want painted, like a nearby vehicle. Lay down drop cloths or newspapers to protect surrounding surfaces from overspray.
#2 Wear Protective Gear: Before handling the cold galvanizing compound spray, put on appropriate protective gear, including gloves, safety goggles, and a mask to protect against inhalation of fumes.
#3 Shake the Can (If Applicable): If you’re using a spray version of ZRC Cold Galvanizing Compound, shake the galv spray paint can vigorously for about one minute to ensure that the contents are thoroughly mixed.
#4 Test the Product: Before applying the compound to the metal surface, perform a test spray or brush stroke on a small inconspicuous area to ensure proper nozzle function and to familiarize yourself with the application pattern.
#5 Apply the Compound: If spraying, hold the spray can approximately 8 to 12 inches away from the metal surface at a 45-degree angle. Begin spraying or painting in smooth, even strokes, moving back and forth to achieve uniform coverage. Apply a thin, even coat of the compound, making sure to cover the entire surface area.
#6 Overlap Strokes: To ensure complete coverage and avoid missed spots, overlap each pass of the spray by about 50%. This helps prevent uneven coating and ensures consistent protection across the entire surface.
It really is that simple!
Future Considerations
Specifying a high-quality cold galvanizing compound can have a significant impact on future project decisions and sustainability. By choosing a superior product, architects ensure that metal components are effectively protected against corrosion, which enhances the longevity and durability of the structure. This proactive approach reduces the need for frequent repairs and replacements, leading to lower long-term maintenance costs and minimizing resource consumption.
Additionally, the extended lifespan of the structure contributes to overall sustainability by reducing the environmental impact associated with manufacturing new materials and disposing of corroded components. Investing in high-quality corrosion protection not only supports the immediate success of the project but also aligns with broader goals of sustainability and resource efficiency in future developments.
Contact Our Team To Learn More About Our Galvanized Paint
With over 70 years of experience, ZRC stands at the forefront of corrosion protection, delivering the highest-quality cold galvanizing compounds that have set industry standards. Our long-standing reputation for excellence is built on providing the best solutions for galvanizing repair, touch-ups, weld repairs, and structural steel maintenance. Cold galvanizing compounds are crucial for safeguarding metal surfaces against corrosion, ensuring both the longevity and durability of your projects. ZRC’s product offers unmatched protection with its high zinc content and advanced formulation, making it the top choice for architects who demand superior performance and reliability.
By specifying ZRC’s cold galvanizing compound, you are not only choosing a product backed by decades of expertise but also reinforcing your commitment to quality and sustainability in your projects. Our team is dedicated to supporting you with the best solutions and personalized guidance, ensuring you achieve the best results with every application.
We invite you to consider ZRC for your upcoming projects and experience the benefits of our industry-leading products firsthand. For further details or to request samples, please contact us directly. Let ZRC’s expertise and high-quality solutions elevate your project’s success.
How Can I Find ZRC Cold Galvanizing Compound Near Me?
ZRC is not found in hardware stores. Our products are highly specialized, and as such can only be purchased directly from our website or by finding a local authorized distributor that has our product in stock.
Option #1 Order ZRC Online: Buy ZRC directly from our web store. One of the most significant benefits of making a purchase online is convenience. You can shop for your needed rust prevention products from anywhere at any time, without having to leave your office or home. Our online store eliminates the need to physically visit a retailer, saving you time and effort. When you do, we’ll ship your product to you within 24 hours!
Option #2 Get It Directly From a Distributor: That’s not to say shopping online is your only option. In fact, many happy ZRC customers get their products by going directly to a ZRC dealer. Our distributors have in-depth knowledge of the products they sell. Shopping online can feel a bit overwhelming if you’re not sure exactly what you’re looking for. Which ZRC product is right for your project? Do you want aerosol spray or brush-on paint? A dealer is able to provide detailed information and guidance on product selection, use, and maintenance.
Our team of specialized experts is a family that has pioneered zinc coating technology. With craftsman-like experience and decades spent honing our products, we are recognized as the world's leader in zinc coating technology.
If you’re worried about rust protection, know that the only product you need is manufactured by ZRC. There’s a reason we’re the industry leader!